Hydro Testing
Hydro Testing :
1.1 Purpose
This procedure specifies hydrostatic testing procedure using inline weld tester and
acceptance criteria of piping works to perform the required level for the Project.
1.2 Scope of Application
This procedure covers pressure testing of newly constructed plant piping and pipelines
which are designed and constructed in accordance with ASME B31.1, ASME B31.3,
ASME B31.4, or ASME B31.8 codes as applicable. Also this procedure covers
mandatory requirements for pressure testing existing plant piping and pipelines for
revalidation purposes or after repairs.
The inline weld tester shall be utilized to conduct hydrostatic testing of the flange butt weld in
accordance with SAES‐L‐ 150 paragraph 5.7.
1.3 Definitions
1.3.1 Category D Fluid Service (As per ASME B31.3): A fluid service in which all the following
apply:
(1) The fluid handled is nonflammable, nontoxic, and not damaging to human tissues.
(2) The design gauge pressure does not exceed 10.55 kg/cm2 as a gauge.
(3) The design temperature is between – 29C and 186C.
1.3.2 Category M Fluid Service (per ASME B31.3): A toxic fluid service in which exposure to
very small quantities of the fluid in the environment can produce serious irreversible
harm to persons on breathing or bodily contact, even when prompt restorative measures
are taken.
1.3.3 Normal Fluid Service: A fluid service pertaining to most piping covered by ASME B31.3,
i.e. not subject to the rules for Category D. Category M and not subject to severe cyclic
conditions.
1.3.4 Calculated Test Pressure: The test pressure determine in accordance with applicable
codes and standards.
1.3.5 Minimum Test Pressure: The lowest allowable test pressure gauge reading (the
calculated test pressure plus the additional pressure resulting from the static head of the fluid).
1.3.6 Maximum Test Pressure: The highest allowable test pressure gauge reading (the
pressure test rating of the “weakest” component in the test system).
1.3.7 References
1.3.8 INTERNATIONAL CODES AND STANDARDS
ASME B 31.3
ASME B 31.4
ASME B 31.8
1.3.9 Relevant Code and Standards
SATIP-A-004-05, Leak Testing.
G.I .2.100 Work permit system
G.I.2.102 Pressure Testing Safety
G.I 447.003 Pressure relief valves, Routine tests and Inspections.
1.4 Units
Unless otherwise specified, metric, Celsius and kilogram units shall be applied as the
measurement system for the drawings and documents to be submitted.
1.4 HYDROSTATIC TEST SYSTEM (USING INLINE TESTER)
1.5 In case of flanged tie-in connections, a flange weld tester shall be applied to conduct
hydrostatic testing of the flange weld. An inline weld tester is applicable localized
testing of flange butt weld only.
1.6 The test shall be hydrostatic using water, except if there is a possibility of damage
due to freezing, or if the operating fluid or piping materials would be adversely
affected by water. Any
1.7 other suitable liquid shall be used with Company approval.
2.3.1 Testing inflammable fluids shall be avoided as far as possible. If it is specifically
required it shall be carried out only with approval of Company.
2.3.2 If a flammable liquid is used, its flash point shall be not less than 50 °C and
consideration shall be given to the test environment.
3 TEST WATER CRITERIA
3.1 Criteria of hydrostatic test water shall be conformed to SAES-A-007.
3.2 Care shall be taken to ensure the use of clean water for hydrostatic tests. The
seawater is prohibited to being used. A suitable filter should be provided in the filling
line to the systems in order to remove foreign mattes such as sand, rust or other
particles in the proposed test water.
3.3 Water used for hydrostatic testing of austenitic stainless steel piping, vessels, and
equipment including those with austenitic stainless steel claddings, linings or internals
(including valve trim shall conform to the requirements listed below. These
requirements apply also to 12 chrome claddings or linings that are welded with
austenitic stainless steel weld filler.
3.1.1 Water containing more than the fifty- (50) ppm chlorides shall not be used.
3.1.2 Water containing more than fifty-(50) ppm but less than two hundred (200) ppm chlorides
shall be treated with an inhibitor of 1.5% soda ash and 1.5% sodium nitrate and re-tested to
ensure the test chloride content is 50 ppm or below
4 TEST PRESSURE
4.1 The test pressure and test method shall be in accordance with approved line schedule
and drawings, which are supplied by Contractor and/or Applicable Codes as referenced
in Paragraph 1.4.1.
4.2 Provision shall be made to facilitate conducting a strength test to the tie-in butt welds
of new piping to either new or existing piping system. The test pressure shall be based on
the minimum required by Code of the tie-ins is to an existing system. If a hydrostatic
testing for the tie-in butt welds is deemed impractical, a request to utilize NDT in-lieu of
pressure testing shall be submitted for approval in accordance with SAES-A- 004 section 6 and
section 7.
4.3 Testing of utilizing a flange tester is to ensure the strength test of the newly weld
flange butt
4.4 weld joint. Service test of the piping system after flanged tie-in to prove the integrity
of the piping system is applicable after the bolt torquing.
5 INLINE WELD TESTER
5.1 The Inline weld tester is used to hydrostatic test the integrity of new or existing welds
where butt welded flange has been added to a pipeline. When a new flange has been
welded to a pipeline, traditionally the method used to prove the integrity of a weld
would involve flooding the pipeline in order to hydrostatic test. Flange test overcomes
this problem as it isolates the testing area, this, reducing time and resources required.
5.2 The flange weld tester can be used on pipes size ranging from 1/2” to 36” and pressure
rating from Class 150 to 2500. Schematic diagram of hydrostatic test using a flange weld
tester with ancillary equipment is attached Appendix I. Specification of flange weld
tester as per attachment.
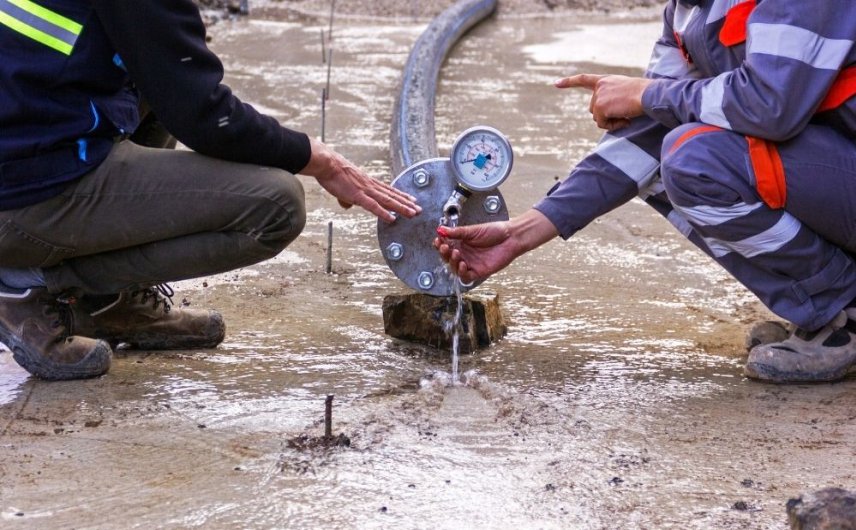
5.3 The Inline weld tester is inserted into the pipeline and the seal are expanded radially
against the pipe bore, either mechanically or hydraulically to seal the weld area. The
sealed area is then pressurized through the fill port with either liquid or gas to the
required test pressure.
5.4 Following ancillary equipment to support hydrostatic test tools shall be utilized.
• Calibrated and certified test gauge
Pressure Gauge (2No’s)
• Calibrated pressure relief valve
• Hydrostatic test pump
• High pressure hose
• Test manifold Etc.
5.5 A Inline weld tester shall be used with temporary gaskets for blanking flat face, raised
face and ring joint type flanges. Used gasket shall be properly disposed and re-use of
gasket is prohibited.
6 HYDROSTATIC TESTING PROCEDURE USING A INLINE WELD TESTER
Operating instructions which provided manufacturer is as per attachment.
6.1 Installation
6.1.1 Verify that the barrier tape and warning signs are in place.
6.1.2 Prepare the suitable flange weld tester with ancillary equipment, such as calibrated and
certified test gauge, hydrostatic test pump, hose, test manifold and etc. All ports
required to operate tool are located on the end of the tool body. The ports are stamped,
(H) Hydraulic Port, (PM) Port Monitor, (F) Fill Port, and (V) Vent Port.
6.1.3 Verify that the test manifold is fitted with a pressure relief valve which calibrated to
specified pressure.
6.1.4 Check and verify the complete removal of welding slugs.
6.1.5 Inspect again the cleanness of existing pipe inside and butt welded flange.
6.1.6 Locate flange weld tester to newly butt-welded flange. In case of large size flange weld
tester, suitable rated lifting and rigging equipment operated by qualified personnel is
required.
6.1.7 Insert and connect flange weld tester with temporary gasket.
6.1.8 Conduct bolt tightening as per required bolt tension.
6.1.9 Activate the seal by either mechanically (by rotating shaft) or hydraulically (using
hydraulic activation pump at set pressure). The seal is expanded radially against the
pipe bore, either mechanically or hydraulically to seal off the weld area.
6.1.10 Verify that the port monitor hose is routed to a safe monitor area and that the open end
of the hose is sub
6.1.11 merged in a bucket of clean water.
6.1.12 Connect a suitably rated hose from the test manifold to the fill port of the flange weld
tester.
6.1.13 Connect a suitably rated hose from the test manifold to the hydrostatic test pump.
6.1.14 Fit the test gauge to the test manifold.
6.2 Hydrostatic test
6.2.1 Verify that the test manifold vent valve is open position.
6.2.2 Operate the hydrostatic test pump until test medium flows from the test manifold vent
valve.
6.2.3 Close the test manifold vent valve.
6.2.4 Verify that the flange weld tester vent port valve is open position.
6.2.5 Operate the hydrostatic test pump until test medium flows from the flange weld tester
to vent valve.
6.2.6 Verify that all the air is expelled from the flange weld tester void.
6.2.7 Close the flange weld tester vent port valve.
6.2.8 Operate the hydrostatic test pump until test pressure starts to increase.
6.2.9 Increase the pressure up to the test pressure which specified in the test package.
6.2.10 Pressure rise is staged with 10 minute holding time (equalization time) at 50%, 70%, and
90% of the test pressure.
6.2.11 On initial pressurization, pressure holds after equalization at 50% test pressure. Gauges
that hold pressure at 50% of the test pressure, and visually check any leaks. Contact
COMPANY after lines shows a successful result at 50% initial pressurization stage for
efficiency.
6.2.12 Upon pressure reach the test pressure, allow the test pressure to stabilize. Care should
be taken not to exceed 5% of the stated test pressure. The relief valve shall be
calibrated accordingly.
6.2.13 Hydrostatic test pressure shall be maintained for a sufficient time to visually
determine if there are any leaks.
6.2.14 Holding period of the test pressure shall be 30 minutes minimum and shall be extended
if deemed by the COMPANY inspector.
6.2.15 Record the test result on pressure test report. (SATR-A-2001)
6.3 Post‐Hydrostatic test
6.3.1 Upon completion, gently bleed down the test pressure.
6.3.2 Verify that the test pressure is at zero.
6.3.3 Open the flange weld tester vent port valve.
6.3.4 Verify that the atmosphere contained by the flange weld tester is at ambient pressure.
6.3.5 Disconnect the hoses and allow the test medium to drain as per SAEP-327.
6.3.6 De-activate the seal by either mechanically (by rotating shaft) or hydraulically (by
bleed down the flange weld tester hydraulic set pressure).
6.3.7 Allow 5 minutes for the tool seals to fully relax.
6.3.8 Loosen the bolts on the flange weld tester.
6.3.9 Remove the flange weld tester from newly butt welded flange. In case of large size
inline weld tester, suitable rated lifting and rigging equipment operated by qualified
personnel is required.
6.3.10 Clean up the Inline weld tester with ancillary equipment
.
6.3.11 Tide the work site and remove barrier tape and warning signs.
6.3.12 Conduct reinstatement works as per isometric drawing.
6.3.13 Conduct bolt touqueing and then service test shall be executed during the start-up
in order to prove the integrity of the piping system.
7 FINAL INSPECTION
When the Subcontractor has completed hydrostatic test, the Contractor shall inspect the
system for reinstatement and shall notify the Subcontractor of any deficiencies or outstanding
work which shall be completed prior to acceptance of the system. If there are no remaining
works, the system shall be accepted by Contractor and Company.
8 TEST RECORDS
8.1 Test result shall be recorded in pressure test report as per SAIC-A-2015, visual inspection
at test pressure for Hydro Testing of Piping System
8.2 Records shall be made of each test package. These records, when completed, shall be
submitted as part of the test and inspection certificates, which are required for precommissioning.
Records shall include;
(1) Date of test
(2) Identification of piping system
(3) Test medium
(4) Test pressure and maintaining time with pressure gauge range and calibration
certificate for 2 gauges.
(5) Test manifold with calibration certificate
(6) Flange weld tester calibration certificate
(7) Relief valve (1 No;s) Calibration certificate
(8) Test pump with calibration
(9) Minimum ambient temperature
(10) Test medium temperature
(11) Pressurizing procedure and apparatus for high-pressure piping (if necessary)
(12) Approval signature of witnesses (Company, Contractor and Subcontractor)
8.3 The test pressure recorders for piping which require that pressure be held for a specified
period of time shall include any corrections of test pressure due to temperature
variations between the start and finish of the test.
8.4 All test records and authorized Contractor certification shall be retained in the test
package records for turnover to the Company. Test database shall be established to
monitor status and progress.
9 TEST COMPLETION
9.1 The hydrostatic test shall be considered complete when;
(1) All defective welds, defective materials, flange leaks, valve gland leaks, or other such
defects have been corrected to the satisfaction of the Company.
(2) All documentation and test package information is completed and accepted by the
Contractor and by Company.
9.2 In the event that repairs or additions are made after the pressure test, the piping shall
be retested at the pressures originally specified for the test.
APPENDIX. I SCHEMATIC DIAGRAM OF HYDROSTATIC TESTING USING INLINE
WELD TEST WITH ANCILLARY EQUIPMENT
(1) Inline weld tester (Calibrated)
(2) Calibrated and certified test gauges (2 No’s) PG Validity -1 Month
(3) Calibrated and certified PRESSURE RELIEF VALVE
(4) Hydrostatic test pump with calibration
(5) High pressure hose
(6) Test manifold with calibration certificate
(7) Relief valve with calibration (Validity of calibration 2 Weeks)